Seeed reServer’s Vapor Chamber keeps this Compact Server Chill 24/7
As the end to Moore’s law approaches, investment into compact and efficient thermal management solutions is heating up. With that, newer and more advanced technologies including Vapor Chamber (VC) cooling are finding their way into more and more devices. One such device is the reServer by Seeed Studio, whose vapor chamber technology enables exceptional performance and longevity in a smaller form factor.
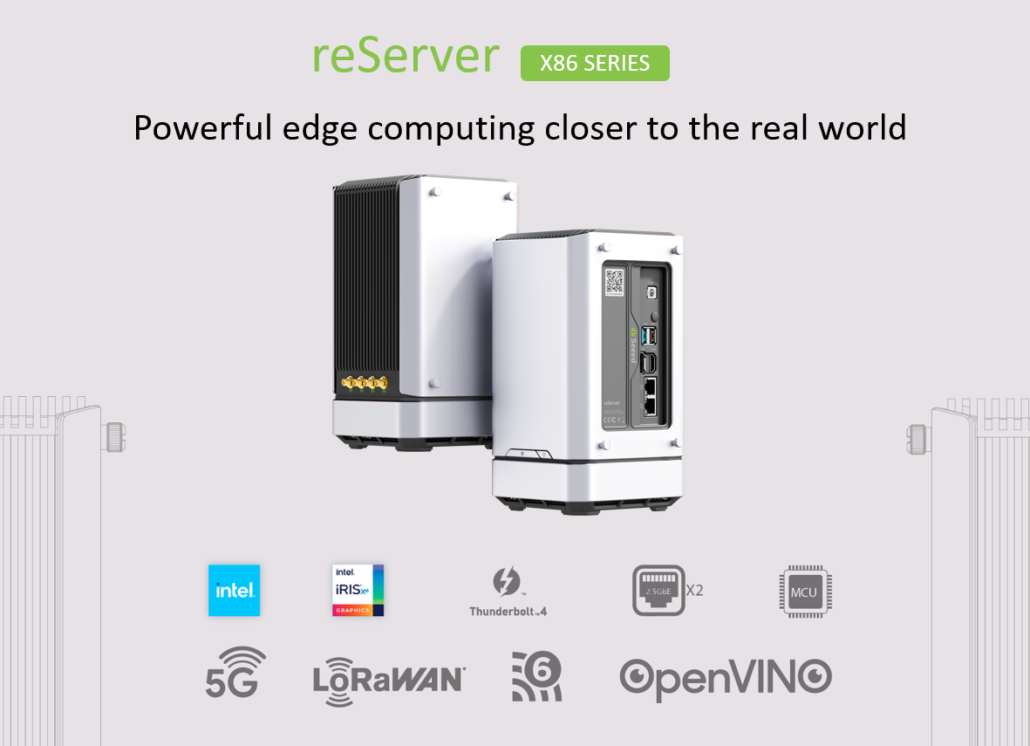
Vapor Chambers are what tubes of liquid flowing in a desktop gaming machine are to a laptop and more recently, smartphones. The first commercial vapor chambers were implemented in gaming laptops and the Asus ROG Phone was the first smartphone to sport a vapor chamber under its hood back in 2018. Fast forward to 2021 and Apple is reportedly planning to incorporate the technology into its iPhones. Popularity in vapor chambers is gaining momentum as technology improves and prices fall, with the technology now branching into other high-performance devices such as servers. The inclusion and size of the chambers are becoming a valued feature in an age where performance is no longer only measured in GHz per second.
While a server in your local infrastructure may not be as space-constrained as your smartphone, or as power-hungry as a gaming laptop, it is likely, despite what your peers may say, that you are not using your phone all the time. For servers, it is vital for them to run constantly throughout the day, month and year with as minimal downtime and disruption as possible, and that generates a lot of heat.
Seeed Studio’s reServer device packs in a lot of functionality in a compact device, including high-speed 2.5Gb Ethernet, hybrid connectivity such as BLE and WiFi, and support for 5G and LoRaWAN. Based on the ODYSSEY X86 v2 board and powered by Intel® Core™ 11th Gen. processor and Intel UHD Graphics or Intel Iris Xe Graphics, reServer is a powerful edge computing device in a small compact package.
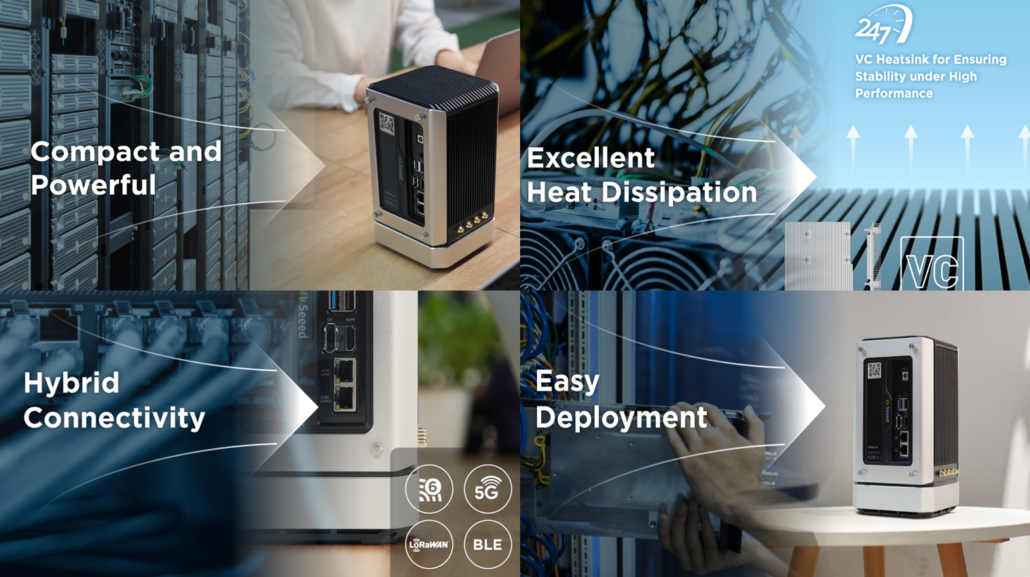
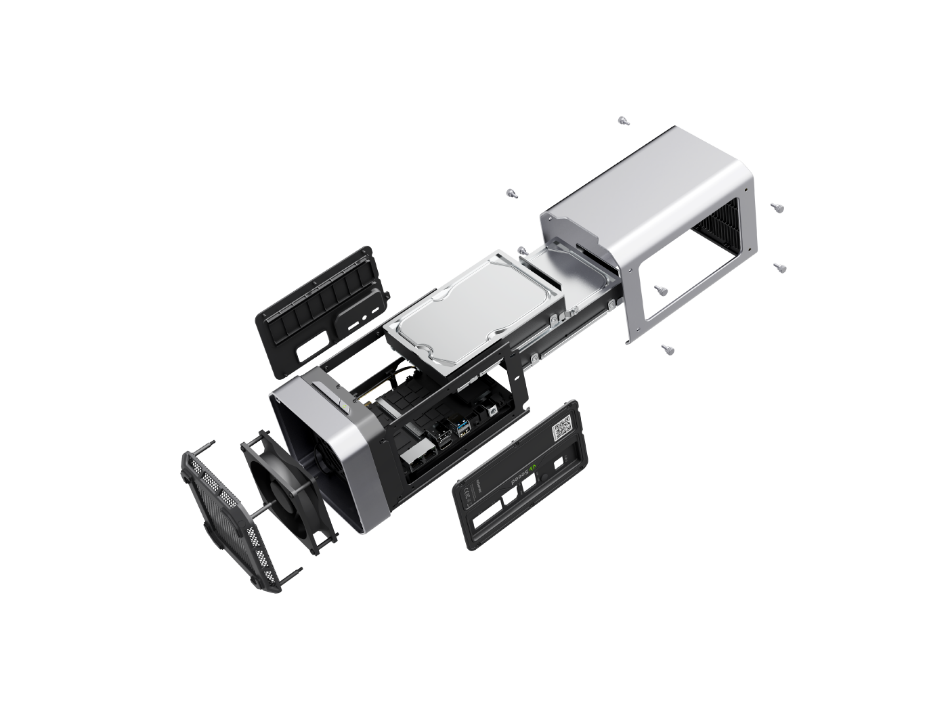
As a high-performance server, reServer pushes the limits when it comes to cooling requirements. The solution is the unique vapor chamber-heatsink (VCH) design that allows grants the server much greater stability when running at high demand. So what exactly is a vapor chamber and how does it improve performance?
How do vapor chambers and heat pipes work?
A vapor chamber consists of a vacuum in a sealed vessel, or envelope such as copper, that is lined with a fine wick structure and contains a small amount of working fluid, typically water that is in equilibrium with its vapor. The chamber can contain internal support structures to prevent the chamber walls from collapsing or expanding under high heat loads. Wicks can be made from a fine mesh or fiber material such as powdered copper welded onto the inner surface or consist of a series of embossed shapes or grooves directly on the copper envelope itself.
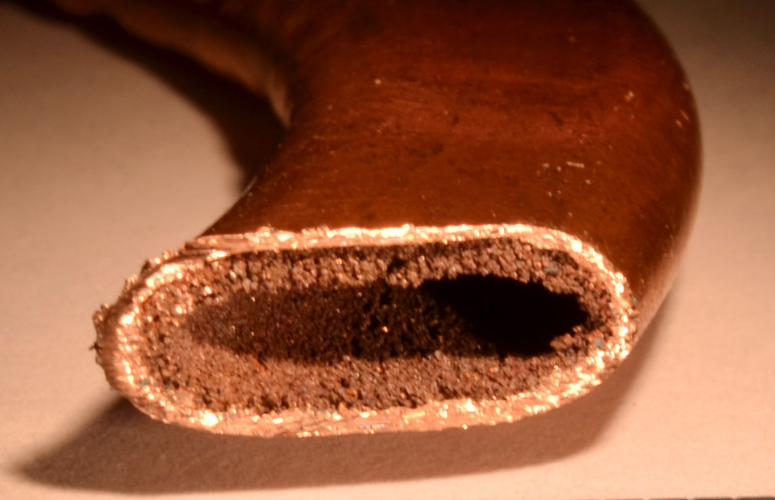
Source: Wikipedia
The working principle of vapor chambers is essentially the same as heat pipes but in a different geometry, and the two share many similarities.
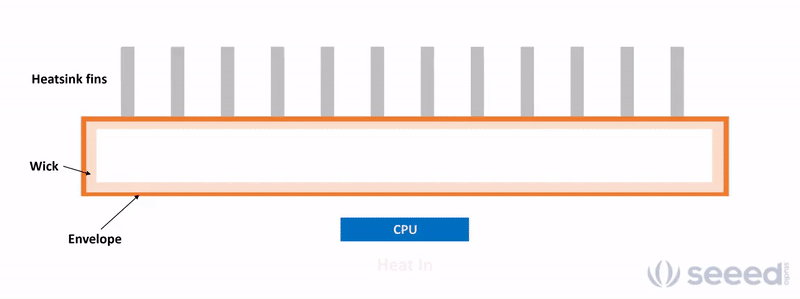
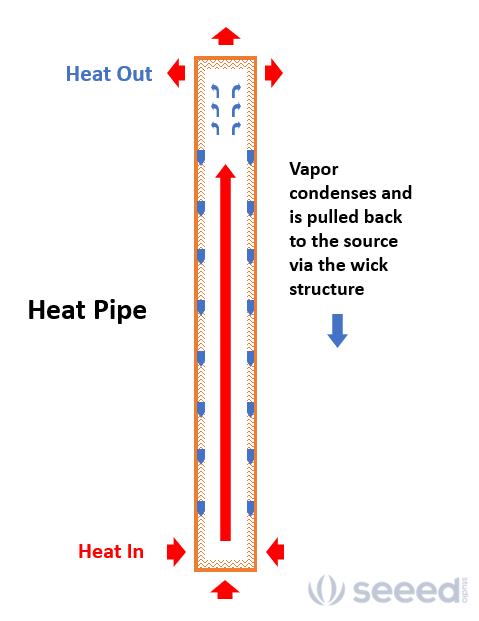
When one end of the heat pipe or side of a vapor chamber is heated by a source, an IC for example, the working fluid evaporates and the vapor travels at high speed to the other end of the heat pipe, or laterally across the vapor chamber. As the vapor cools, it transfers its stored energy to the envelope, which then either directly dissipates to the environment or conducts to additional cooling devices such as a solid copper or aluminum heatsink. Upon losing its energy, the vapor condenses back into a liquid onto the wick structure, which then transports the fluid back to the heat source via capillary action – imagine a dry kitchen towel absorbing a drop of water. The cycle then repeats. The result is high-speed heat transfer and a low temperature gradient across the heat pipe or vapor chamber.
Heatpipes and vapor chambers are known as passive two-phase devices. They use the high latent heat of the working fluid, or the energy required to cause a phase change from liquid to gas and vice versa, as a means of storing energy, then use the strong pressure difference across the envelope to transport energy at speeds hundreds of times faster than solid conductors. Copper is one of the best metal heat conductors with thermal conductivity of around 400 W/(mK) (watts per meter-kelvin), however passive two-phase devices have effective thermal conductivities of 3200 to 200,000W/(mK) depending on the type of wick structures, working fluid and the design of the inner chamber.
What is the difference between vapor chambers and heat pipes?
A vapor chamber is a planar 2D heat pipe, in that they are effective at transferring heat evenly across an area rather than a length and subsequently can be designed to fit into tight spaces such as behind a phone’s battery. They are heat spreaders, moving heat from a concentrated area of high heat flux to a much larger area, thus reducing heat flux. Heat pipes on the other hand, transport heat in one direction and so are good for transferring heat from the source to another area that may be more suited to dispersing the heat, e.g. a heat pipes may transfer heat from CPU to the edge of the casing where fans can blow the heat out. Heat pipes are much cheaper but have restricted geometries.
Advantages of vapor chambers:
- Highly efficient and uniform heat spreading across 2D space. 40% more effective thermal performance compared to a thin copper plate of the same size.
- Flat and geometrically flexible, can fit into very thin spaces. Only a few millimeters thick.
- Suitable for high heat flux applications up to 350W/cm2 and even greater with advanced wick designs.
- Direct contact interfaces using heat pipes use solid metal brackets and so are not as effective at spreading heat compared to vapor chambers, which, due to the flat geometry, maximize the area of the chamber in contact with the source.
- Performance is not affected by gravity unlike traditional water pumping systems for example.
The performance benefits of vapor chambers are vast, perhaps the only major disadvantage is the cost due to the complex production process involving 20 or more individual steps. Traditional vapor chambers are made of two pieces of metal that must be welded together on all four sides to form the chamber and may contain internal posts for structural support. These additional processing steps increase the cost compared to heat pipes or hybrid 1-piece vapor chambers – which are essentially flattened heat pipes. So, despite the increased efficiency and performance, vapor chambers will not phase out heatsinks or heat pipes any time soon.
Seeed reServer’s vapor chamber

Seeed’s reServer has a large 2 piece vapor chamber heatsink (VCH) with an area measuring 136 x 92mm in size, about the same size as a 3.5-inch hard disk drive. The outside exoskeleton is made of aluminum and encases the copper vapor chamber. The vapor chamber has rows of structural supports, whose indentations are slightly visible on the aluminum surface. These supports and the casing allow the chamber to withstand high clamping pressures and deformation under high temperatures.
A small area similar in size and shape as the Intel® Core™ chip protrudes out from the vapor chamber side and a spring-loaded screw sits on each corner. The screws can be tightened to ensure a tight and uniform fit between the VCH and the IC. A zipper fin heatsink is bonded directly on the other side of the vapor chamber with the vapor chamber serving as the base of the heatsink, further reducing volume.

The vapor chamber spreads the heat from the small area of the IC throughout the vapor chamber where it then conducts through the fins of the heatsink. A large fan at the base then pushes the air out of the perforated bottom. All these thermal management elements work together to provide exceptional cooling performance compared to other solutions.
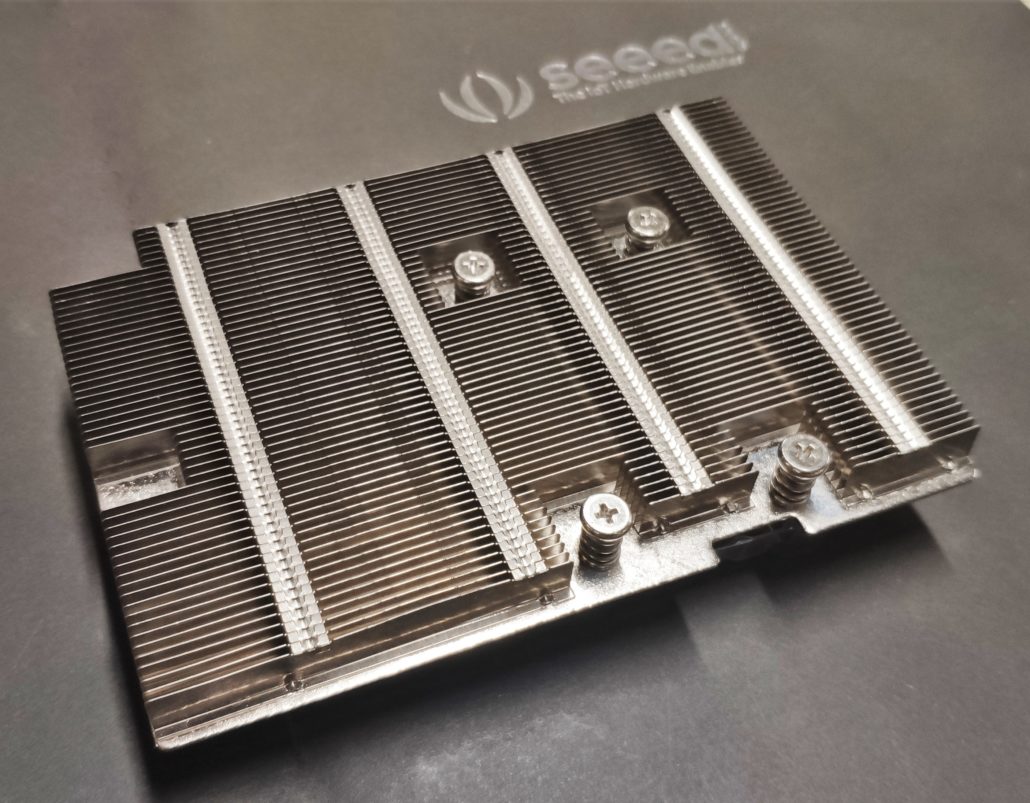
Before settling on VC technology, Seeed’s research and development engineers tested a variety of similar passive cooling solutions including different combinations of solid aluminum heatsinks and two-phase devices. Ultimately, the vapor chamber with the heatsink came out on top in terms of heat transfer when connected to a heatsink of the same size. With the VCH, the CPU is capable of running at a maximum power of 28W.
Thermal Analysis
The temperature rise or the temperature gradient between two points is the product of the power and the thermal resistance of the device, theta θ. It therefore follows that to run more power-hungry machines we need to reduce θ as much as possible.
∆T = P × θ
Similar to electrical resistance, thermal resistance in a path can be modeled in a series fashion, where the total thermal resistance is the sum of all thermal resistances in the path. For example, the thermal resistance of the IC to the heat sink and heatsink to the environment.
θja = θjc + θca
Here θjc is the thermal resistance from the junction to the case, where the junction (j) is the hottest point on the IC, and the case (c) is the device package. θca describes the thermal resistance between the case and ambient (a), or the environment. We cannot control the inner workings of the IC, but we can control the path to ambient, by adding low resistance interfaces and components, for example, ensuring direct contact to the IC and adding heatsinks.
Thermal resistance also changes with the available airflow, which is typically quoted as the volume of air moved in cubic feet per minute (CFM) for heatsinks.
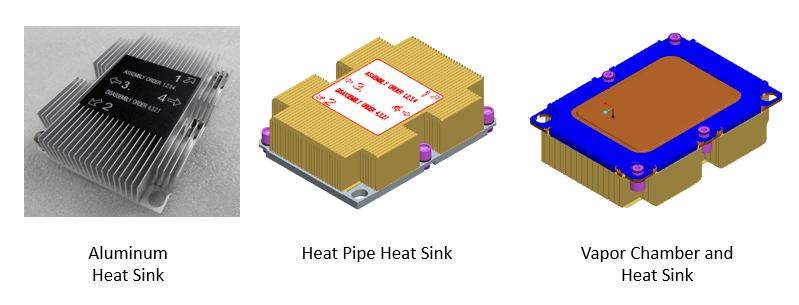
The following chart shows the performance of three cooling solutions; a basic aluminum extrusion heatsink, heat pipe fan stacks and vapor chamber heatsink combination for the same volume.
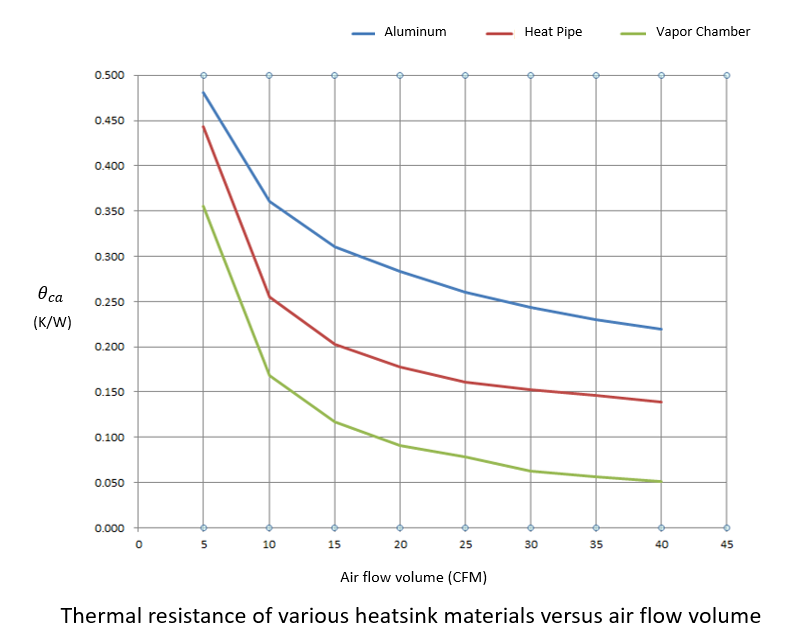
Clearly, the vapor chamber offers much lower thermal resistance compared to the other technologies. Switching from the aluminum heat sink to heat pipe fin-stack, to the vapor chamber saw consistent reductions in the case to ambient thermal resistance across a range of airflow volumes, decreasing it by over two-thirds in some cases (68%). This superior performance allows reServer to run at higher power over long periods, perfect for long life and uninterrupted service.
You can find out more about reServer and inquire pricing on Seeedstudio.com. Currently, the Intel® Core™ i3 version with 8GB and 256 SSD storage, or 16GB and 512GB SSD storage are available.
Your article is very useful, the content is great, I have read a lot of articles, but for your article, it left me a deep impression, thank you for sharing.